Macy’s three-point transformation plan to combat sliding market share — dubbed the “Bold New Chapter” — will rely heavily on its supply chain.
The retailer plans to close distribution centers, increase automation, and implement other tactics that help the corporation improve inventory, productivity, and, ultimately, sales, the corporation's CFO and COO, Adrian Mitchell, said in a Q4 earnings call.
Altogether, supply chain efforts should result in $100 million in cost savings in the current fiscal year, eventually rising to annual run-rate savings of some $235 million by 2026, Mitchell added in the late February call.
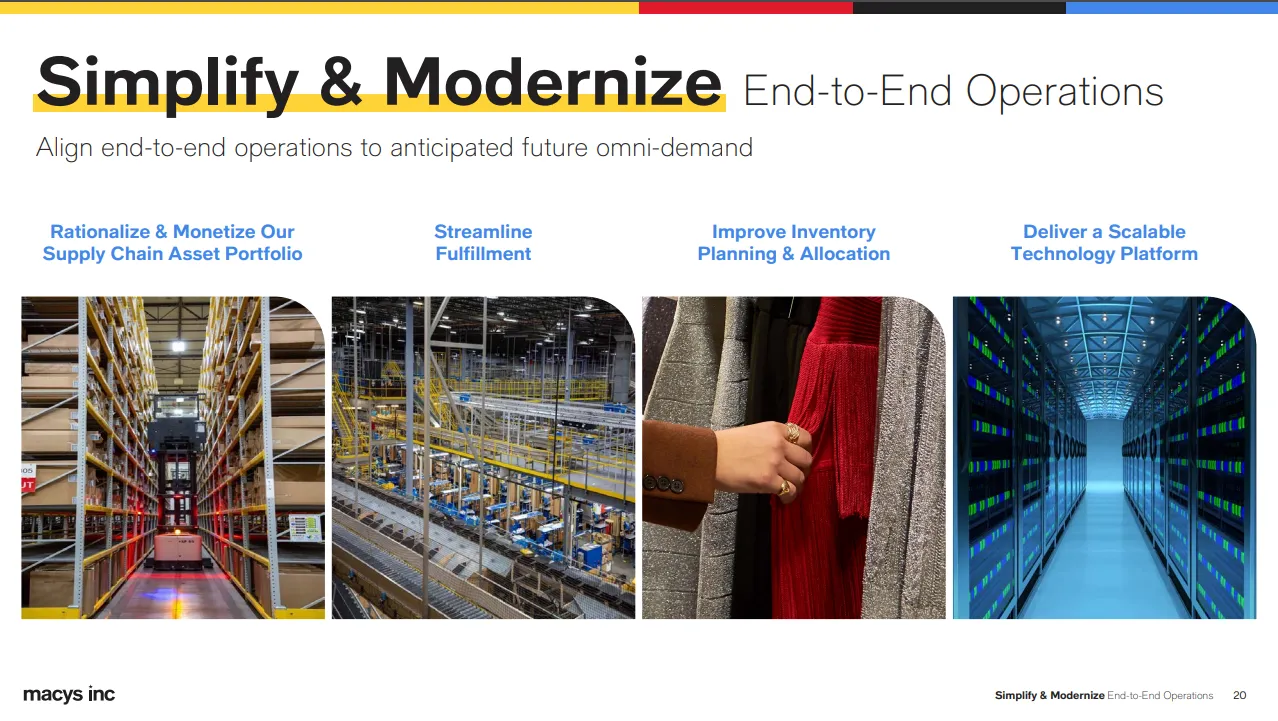
"Across the organization, Macy’s, Inc. plans to align operations to anticipated future omni-demand and deliver a more efficient operating model that will allow the organization to better serve customers," the company said in a press release about the new strategic priorities.
The initiatives come after Macy's reported a $71 million net loss in the most recent quarter. In addition to supply chain efforts, its three-point plan also involves closing some Macy’s stores and investing in the company’s luxury offerings.
They also follow the departure of Macy’s first-ever chief supply chain officer, Dennis Mullahy. The leadership change was a critical moment for the company’s operations: After Mullahy left last July, Macy’s decided not to maintain a CSCO title. Instead, it opted to have its supply chain executives report to Mitchell — who is leading the end-to-end operations initiatives.
Under Mullahy, Macy’s built up infrastructure to bolster omnichannel, including in-store fulfillment. Now, the retailer is pursuing a “right-sized distribution center network,” as Mitchell said on the earnings call.
In doing so, CEO and Chair-elect Tony Spring told investors the retailer plans to monetize $600 million to $750 million of assets, primarily related to the closures of stores and certain distribution centers.
At the same time, the company is already implementing more automation across the Macy’s Inc. portfolio. It is consolidating its vendor base to decrease dependence on expensive digital tools, moving most of its applications from on-premise to the cloud, and building artificial intelligence and other data capabilities for inventory allocation, forecasting, pricing and other functions.
“The inventory planning and allocation changes underway should help improve how we flow products from vendors to customers. They should provide quick replenishment in stores and fulfillment centers, reduce split shipments and lead to higher in stocks, particularly for best-selling items,” Mitchell said.
Macy’s isn’t the only retailer streamlining its supply chain operations in the name of efficiency. Walmart recently offloaded its intermodal assets to J.B. Hunt Transport Services, likely to reduce costs associated with owning a private fleet. Meanwhile, Wayfair is planning to roll out consolidated delivery options, which will help cut shipping costs.
“A modern operation is our objective throughout the company, aligning to the anticipated future omni demand provides synergistic cost savings and allows us to improve our ways of working,” Spring said.